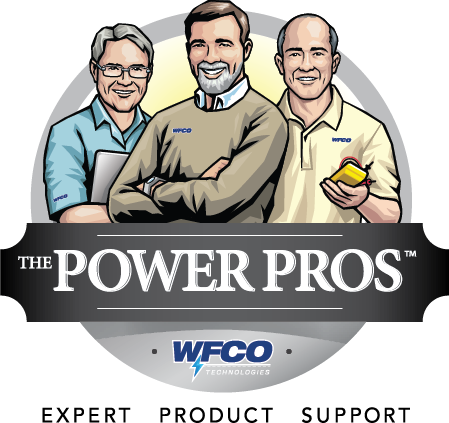
Connect with Power Pro Support
Our Power Pro support team has a combined 50+ years of technical experience. When you connect with us, you’ll get real-world advice that works.
Contact WFCO Technologies
Get in touch with our team for product support, warranty assistance, OEM/distributor sales inquiries, or just to drop a friendly hello. We’re standing by to treat every customer as part of the WFCO Technologies family.